NTSB Grills Boeing Over Max 9 Door Plug Loss
Aircraft giant addresses its manufacturing process during the first day of hearing in Washington, D.C.
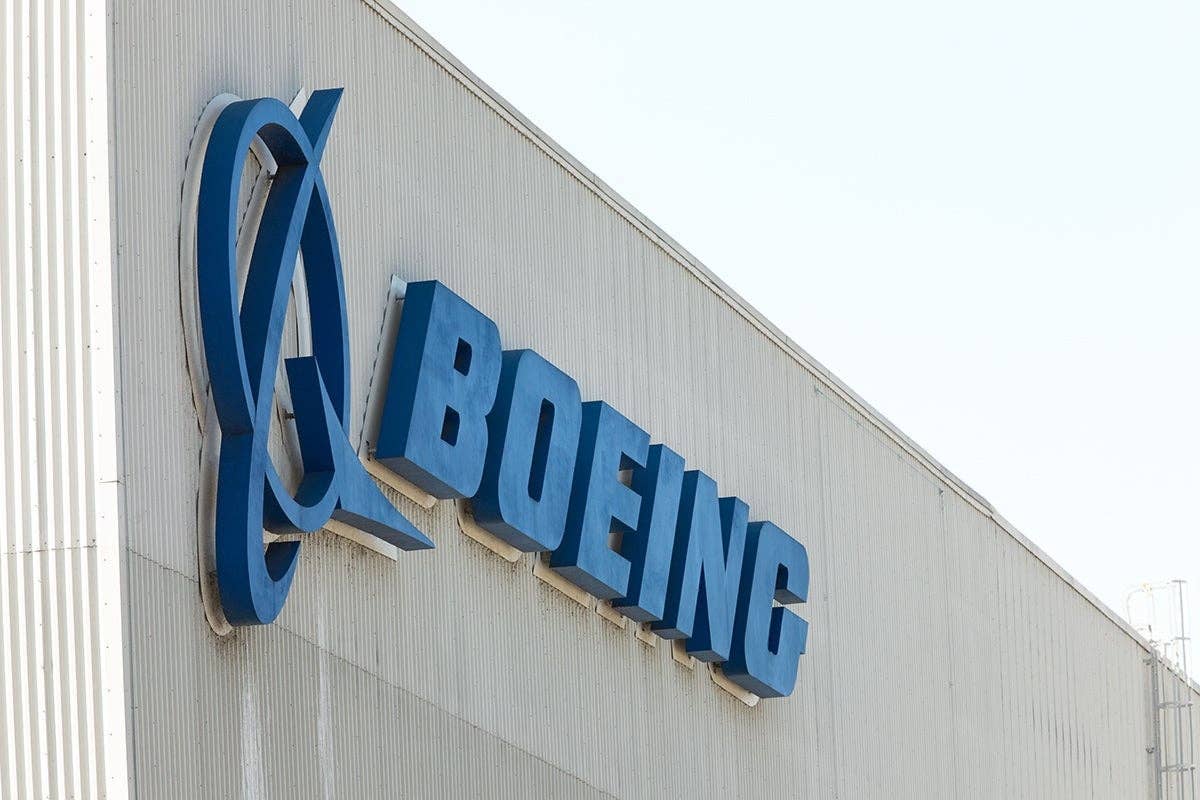
Boeing is testifying at a two-day NTSB hearing in Washington, D.C. [Shutterstock]
On Tuesday in Washington, D.C., the National Transportation Safety Board heard testimony from Boeing officials and contractors from Spirit AeroSystems that painted a picture of a chaotic workplace where the drive to meet production goals was making employees work so fast that mistakes were frequent and assembly did not pass quality inspection.
Wednesday is Day 2 of the NTSB hearing about the loss of a door plug from a Boeing 737 Max 9 in January after takeoff in Portland, Oregon.
According to Tuesday’s proceedings, sometimes the shoddy work was discovered and rectified before the aircraft was delivered. Sometimes it was not, as in the case of the 737 that was delivered to Alaska Airlines.
Boeing relies on contractor SpiritAeroSystems to build the fuselages. A representative from Spirit told the NTSB that the door plug for fuselage No. 8789, which was delivered to Alaska Airlines in fall 2023 and became ill-rated Flight 1282, was built at SpiritAeroSystems Malaysia and shipped to Wichita, Kansas, where it was installed in the fuselage, which was then shipped to the Boeing factory in Renton, Washington.
When it arrived at the factory, it was determined that the rivets in the assembly if the fuselage were substandard, and in order to replace them, the door plug had to be removed.
According to Elizabeth Lund, senior vice president/quality of Boeing Commercial Airplanes, when there is a need to replace a component such as a door plug, there is supposed to be a paperwork trail to indicate what needs to be done and who will do it, and then who has done it.
"We have still found no paperwork documenting the removal of 8789 left-hand door plug," Lund testified to the NTSB on Tuesday.
Lund said the door plug was removed to replace a line of rivets that were not up to standard, and then it was put back into position so that the aircraft could be moved outside and its interior protected from the weather. The door plug was missing four crucial bolts.
According to Boeing, under normal circumstances, the paperwork trail would let employees know the door plug had been reinstalled but the bolts had not been replaced. The paperwork would indicate the bolts had to be reinstalled before the aircraft could be delivered.
That was not the case here, according to testimony. The aircraft was delivered to Alaska Airlines in October 2023 and flew for approximately 100 flight cycles (takeoffs and landings) with the door plug kept in place by a series of small pins. There were two reports of crew noticing pressurization warning lights in the cockpit. The aircraft was supposed to go in for maintenance at the end of the duty day on January 5.
There were Spirit employees at the Boeing Renton plant, but according to testimony, communication between the Boeing and Spirit workers on the floor of the factory wasn’t good, and there was a lot of turnover at the facility because of low morale and early retirement of more experienced technicians due to COVID-19.
There were no serious physical injuries when the door plug blew out as the aircraft reached 16,000 feet, although seven passengers and a flight attendant were treated for injuries upon landing. The flight crew was praised for its skill, and aviation experts noted that had the aircraft been higher, the outcome would have been much worse.
NTSB Chair Jennifer Homendy offered an apology to the passengers and flight crew on behalf of the agency.
The decision to conduct the two-day hearing into the event is unprecedented. Within hours of the blowout, Alaska Airlines grounded its 737 Max 9s, and the FAA followed suit grounding the world fleet for 19 days while inspections were done to door plugs.


Subscribe to Our Newsletter
Get the latest FLYING stories delivered directly to your inbox