In Depth with JoeBen Bevirt Illuminates the Joby Vision
In the quest to free vertical flight, the engineer makes good on a childhood dream.
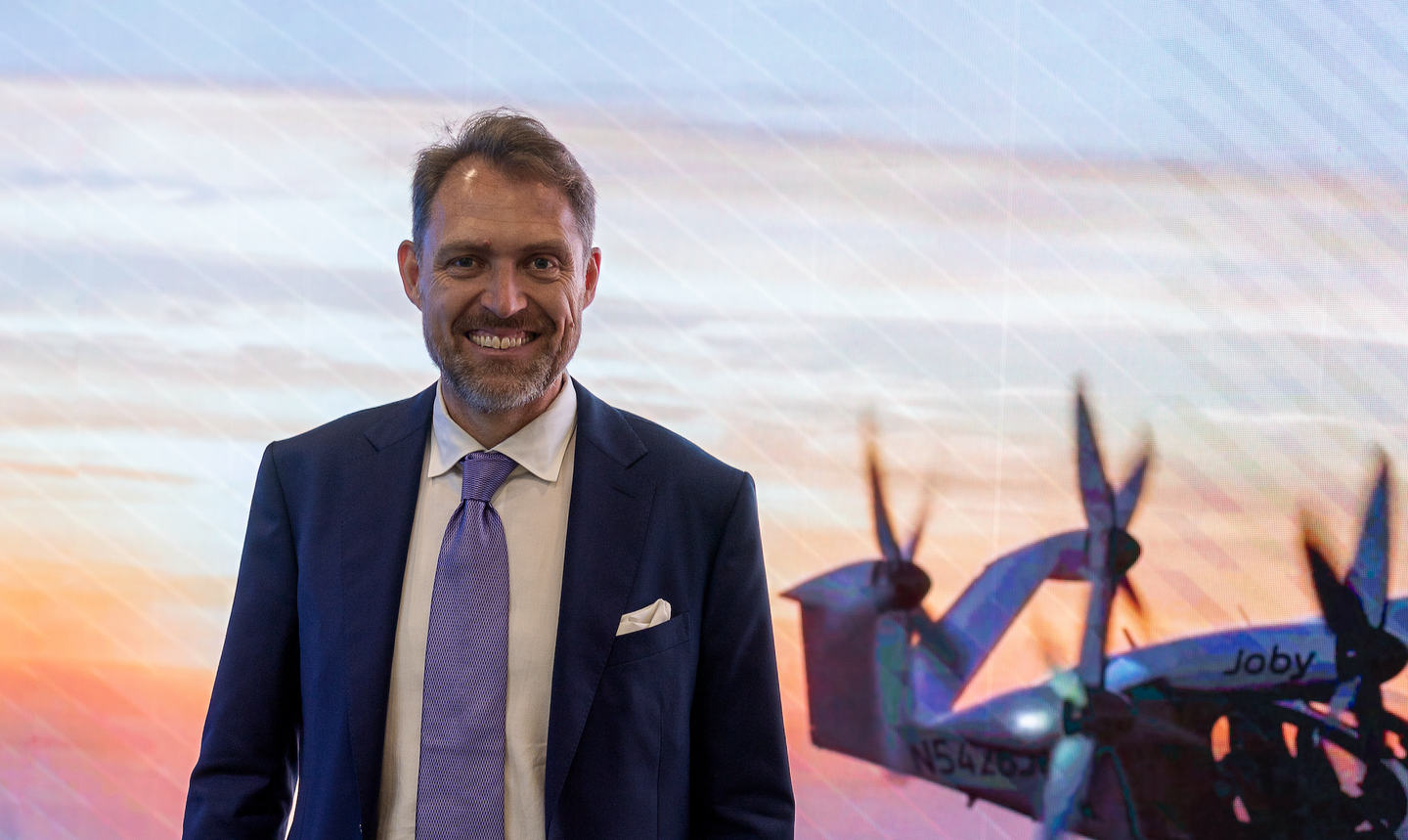
JoeBen Bevirt spoke with FLYING at the Paris Air Show 2023. [Credit: Stephen Yeates]
In the folds of the Santa Cruz Mountains in California, a boy grew up dreaming of a different kind of flight—one that wouldn’t be constrained by the traditional means of lifting off and landing in challenging places, just like the remote enclave his parents called home in the 1970s and ’80s. Yes, helicopters would, in theory, take him where he wanted to go, but the noise produced by a typical combustion engine and rotor blades shattered the quiet he wished to preserve.
This dream provoked a vision for JoeBen Bevirt—one he has singularly pursued ever since.
After finding his natural engineering mind on a track at the University of California-Davis, and a graduate degree in mechanical engineering at Stanford University, Bevirt founded a series of successful companies in the tech sector. He started Velocity11 in 1999, developing robotic systems for laboratory work. The first iterations of “Joby”—Joby Inc., which produced the Gorillapod, and Joby Energy, focused on aerial wind turbines—came into being prior to the main event, Joby Aviation, which he founded in 2009.
Joby Aviation launched to coalesce Bevirt’s vision of an all-electric vertical takeoff and landing (VTOL) aircraft and the transportation system to support and deploy it. Now, as the company surpasses 1,400 employees and celebrates the reveal of its conforming production prototype, the vision sits on the cusp of being fully realized. FLYING talked with Bevirt to illuminate the source of that vision and where it will take Joby next.
FLYING Magazine (FM): So what was it that set off that spark for you when you were that young boy?
JoeBen Bevirt: (JB): I was born and raised far from civilization in a place called Last Chance. Our house was at the edge of a beautiful meadow with fruit trees and a garden nestled among the redwoods overlooking the Pacific Ocean. In the morning I would get a ride to school with one of my parents on their way to work. In the af- ternoon I would either go to a friend’s house and wait or I would take the city bus to the transit station and then take another bus up the coast. I would get off at the bot- tom of Swanton Road and then walk a mile up to Last Chance and then the 4 miles back from Last Chance to my home. It gave me a lot of time to dream about bet- ter ways [of] getting from [point] A to B. I loved where I lived, and I loved my school, but I wanted to be able to expediently get between them.
I imagined an aircraft could take off and land in the meadow. But it was also pretty quiet, and peaceful, and the idea of a really loud aircraft didn’t appeal to me. For me, it was a question of “how do I build an aircraft that is suitable for this serene, beautiful place but that I can take off and land vertically?”
FM: How did you first try to solve that problem?
JB: I inherited my uncle’s collection of model airplane parts including a whole bunch of little model engines—and they were horrifically loud. So, I thought, this is not the answer. They were really fun but really loud. [laughs] Then I started playing with remote-control car motors, and at this point in time, they were these little brushed motors and NiCad batteries, and I mounted props to them, and built many crazy contraptions. This was one of my first experiences with iterative engineering even before I knew what engineering was.
FM: You began working with electric motors, but it took time for them to reach a usable capacity, right?
JB: In 1993 when I was in college, my proficiency with engineering had improved, and I had the opportunity to work for a company doing pioneering work on vertical take off and landing aircraft. Unfortunately, they were horrifically loud. I became convinced that electric propulsion was the critical unlock to make VTOL aircraft part of daily life. NiCad batteries had gotten to 40 or 50 watt hours per kilogram, and there were rumors that the lithium-ion battery was going to move from the lab into production and that Sony was getting close with a cell specific energy of 70 watt hours per kilogram. But even 70 watt hours per kilogram didn’t feel sufficient for a useful endurance.
There were researchers at the DOE [Department of Energy] projecting that lithium ion had the potential to get us to 200 watt hours a kilogram in 20 years. Batteries had been improving by 6 percent a year since the late 1800s, and I figured that it was going to stay on that ramp. But I was 19 years old, and I was thinking, 6 percent a year—it’s going to take 20 years to get to a useful specific energy— that felt like an eternity, and so I put my dream of electric
flight on hold. At Stanford in 1998, I met a guy named JB Straubel who was fixated on building an electric car, and over the years I had the opportunity to experience a few exhilarating test drives in his prototypes. This gave me a front-row seat to the progress being made on batteries. By 2008 I had sourced batteries with a specific energy of 170 watt hours per kilogram and a specific power of more than 1 kilowatt per kilogram, which I believed was sufficient to build a vertical takeoff and landing aircraft with 100 miles of range. After a bit of design work and analysis, I founded Joby to bring electric vertical takeoff and landing aircraft to life. Today we are certifying our aircraft with cells that are more than 280 watt hours per kilogram. And we’ve moved from the idea of making something for an enthusiast to something that could be a new mode of transportation.
FM: So, with that early introduction into electrical and mechanical engineering, it was pretty clear that was your passion. Were there any other directions you thought about going?
JB: No. I loved building things and creating things. But there were no engineers in my family. I remember in seventh grade, my math teacher said, “You’re gonna be an engineer,” and I said, “I don’t wanna drive trains!” and he’s like “No, no, no, no, no...my son’s studying to be an engineer, and I think that you’re going to be an engineer.” And he explained what an engineer was, and I’m like, “That’s it!” So I had my calling since I was really little, but I first had somebody put a name to it in seventh grade. From that point, I was on cruise control, so focused. In high school, I was also really into cycling, so I designed and built one of the world’s first full-suspension mountain bikes, and it was really fun to watch the cycling industry emerge. It was funny back then because all my friends would make fun of me for putting a suspension on a bike, and I said, “But it’s so much better!” And they thought I was weak, like your legs are supposed to be the shock ab- sorbers. But it’s fun to have watched that industry evolve.
FM: So, in graduate school, were there mentors or fellow students that you worked with on the vision?
JB: Right at the beginning of my sophomore year, I went to the dean of the engineering school and said, “You’re teaching computer-aided design wrong. And you’re do- ing a massive disservice to the students, and we have to fix it.” And he said, “‘OK, that’s amusing.” And so he picks up the phone, “Paul, I’ve got somebody for you. Can I send him over?” Click. I ride over to the research park, and I knock on the door, and it says Moller International. There was something that went off in my head, but it didn’t really click. And I walked inside, and there was a picture of this vertical takeoff and landing aircraft, and I’m like— wow! And so it was serendipity.
So I went and interned for Paul [Moller] for a quarter, and then I convinced him that I should create an internship program. I had four interns for the next quarter. And then I convinced him that we should expand and have like 12 interns, and this was with a team of like 40 engineers at the time—awesome engineers—and all of a sudden there were 12 interns and the engineers were looking at themselves wondering, “What just happened?” It was my first experience of leading a larger team. Moller had built a whole bunch of breakthrough vertical takeoff and landing aircraft through the ’70s and ’80s. It was cool for me to be able to see the integration of composites and mechanical engineering and electrical engineering and software engineering—and what was needed to...make vertical takeoff and landing aircraft possible.
FM: You’ve built a company centered around a vertically integrated enterprise. You’re not just making the part— you’re figuring out is this the right composition of this base material. Why is having that depth of control over the process critical to the transformative thing that you’re trying to do?
JB: I think to engineer and build the most performant things—whether that’s at the aircraft level or whether that’s at the system level or the component level, or the individual part—you really need to understand all the nuance[s]. And whether that’s in the material properties or that’s in the way that the pieces integrate together, [or] whether [it’s] the way that the systems communicate with one another. I think that one of the pieces that I’m so excited about and passionate about is the technology that runs both the electronics and the software that run each of the components and the controls, whether it’s the flight computers or the actuators or the air data systems or the navigation systems. All of these different systems across the aircraft share a common hardware and software stack. It gives us the ability to innovate and to move aviation to the next level from a technological standpoint. The rate at which we’re able to collect data from each of those devices, the richness of the data, the temperatures and the currents and the voltages and the acceleration levels...we know so much about everything that’s going on across the aircraft...which is valuable from a product maintenance standpoint...and [provides] the ability to really understand the aircraft at a substantially more sophisticated level than we’ve ever been able to do before.
It also enables us to build a fly-by-wire control system [that] we hope will substantially improve safety by reducing pilot workload and allowing the pilot to focus on things that pilots are really good at doing. Our aircraft—you could just design it in a way that had more pilot workload than traditional aircraft. But we’ve decided to make it substantially easier and safer to fly.
FM: You’ve built a transparent culture. Is this something that you’ve driven into your organization purposefully?
JB: I think because we grew the organization organically, with that as the ethos from the beginning, I think that helps you see it [and know it’s something] that you always have to continue to nurture and focus on and foster, but it is something we cherish.
FM: Were there any challenges with getting the FAA to ac- cept and get through the first set of papers, putting it all into motion?
JB: We started working informally with the FAA back in 2015. We had conversations well back before that, but by that point in time, there was momentum building. We started the Electric Propulsion & Innovation Committee [EPIC] at GAMA. We then began a formal certification in 2018. We’d been flying our full-scale prototype for a [little more than a] year at that point, and the level of engagement and forward lean from the FAA was increasing steadily. We’ve continued to foster a really constructive relationship with everyone that we work with at the FAA. The degree with which the FAA has leaned into this industry is really fantastic. I mean, they see it as you see it, that it has the potential to transform flight both in the degree of relevancy that it has to large por- tions of the population on a daily basis but also to make it safer. And... more accessible, sustainable. So there’s a lot of value in each of these different dimensions.
FM: Can you pick a specific challenge so far that you’ve solved that has curved things up?
JB: I think that the one right now that I’m super excited about is getting this first aircraft off our pilot manufacturing line. And that it is just so exciting to have used all of our quality processes and have built all the procedures to not just build the experimental aircraft but to have the pieces in place to begin building conforming aircraft. So it’s a monumental achievement from the team. It took a spectacular amount of work, and I’m just so proud.
Quick 6
Is there anyone living or dead that you would most like to fly with?
Kelly Johnson
If you could fly any aircraft that you haven’t flown yet, what would that be?
The F-22
What is your favorite airport that you’ve flown into?
Orcas Island Airport (KORS) in Washington
What do you believe has been the biggest innovation breakthrough or event in aviation?
Frank Whittle’s invention of the turbine
What is one important life lesson from being a pilot and inventor?
Dare to look over the horizon.
When not working towards the first TCed eVTOL aircraft, what would you rather be doing?
Catching up on the latest from our advanced research team
This profile first appeared in the August 2023/Issue 940 of FLYING's print edition.


Subscribe to Our Newsletter
Get the latest FLYING stories delivered directly to your inbox