Lilium Begins Testing Electric Jet Power Systems
The manufacturer put the aircraft’s electrical power system, comprising 30 engines within flaps on the main wing and canard, through a series of simulations and tests.
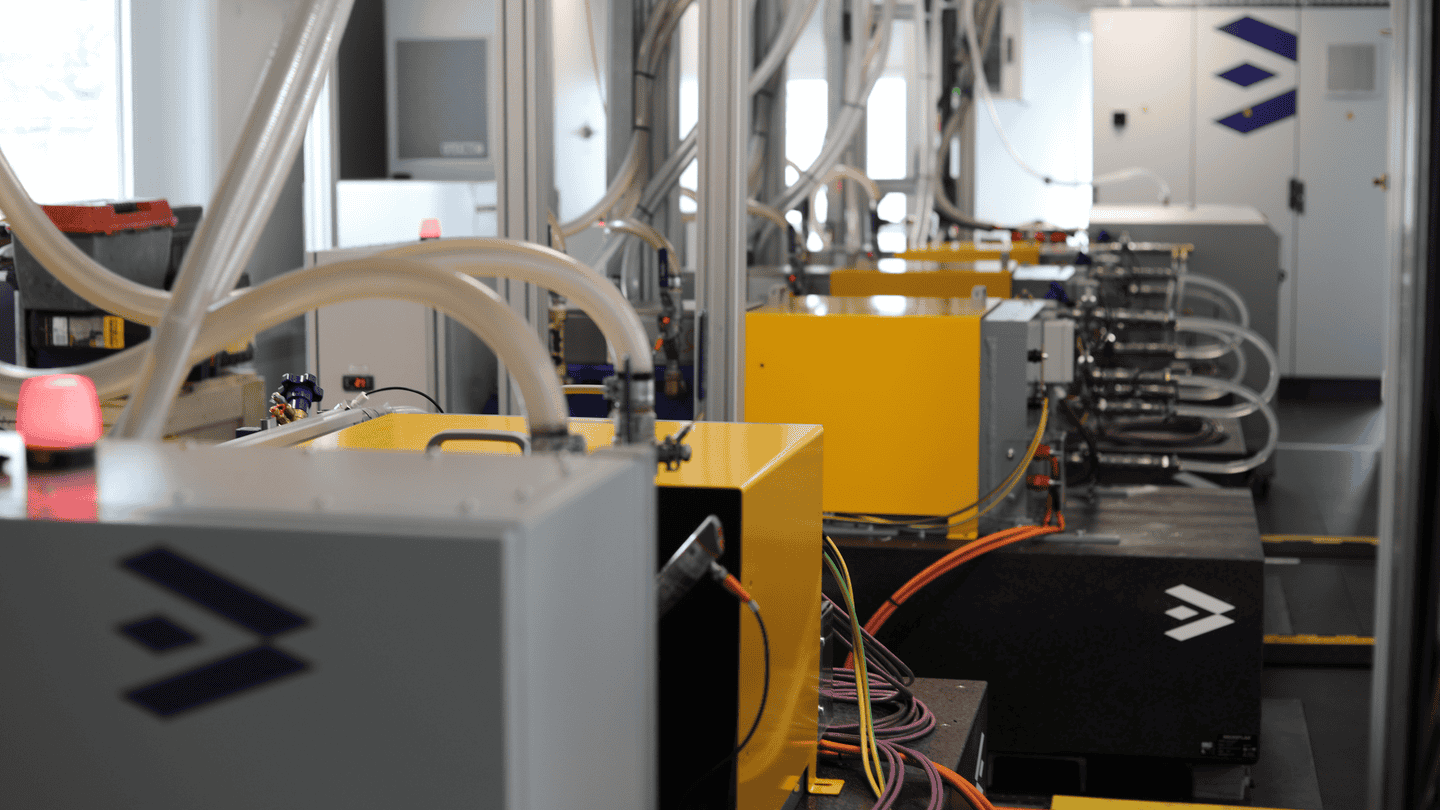
Lilium is running tests on the Lilium Jet’s powertrain at its electrical power system lab outside Munich, Germany. [Courtesy: Lilium]
At a purpose-built laboratory on the outskirts of Munich, German manufacturer Lilium has begun testing the electrical power systems that will juice up its vertical takeoff and landing (VTOL) jet.
The company on Wednesday announced it completed the first stage of power system integration testing, during which the technology was put through a series of simulated flights in a controlled environment.
As the firm works to manufacture its first two Lilium Jets, which it began assembling in December, these tests will help it demonstrate the aircraft’s powertrain performance and safety to the European Union Aviation Safety Agency (EASA). It seeks to certify the design under the regulator’s Special Condition for VTOL (SC-VTOL) rules by 2026 before rolling it out to customers worldwide.
The Lilium Jet’s powertrain comprises 30 battery-electric engines within flaps on the main wing and canard, which stow during cruise flight. Honeywell and Japan's Denso are the main suppliers for the engine components.
The unique configuration is designed to give the aircraft the speed of a jet—about 154 mph (134 knots)—with the vertical takeoff and hover capabilities of a helicopter. Fully charged, Lilium expects it to be able to carry six passengers plus a pilot on city-to-city trips as long as 109 sm (95 nm).
The company’s electrical power system lab, located at its headquarters and test campus, was developed with help from aerospace testing specialist EN4 using software and hardware from test equipment provider NI.
According to the manufacturer, it has the ability to replicate the entire Lilium Jet powertrain from battery pack to engine. The lab’s low voltage systems can power the aircraft’s avionics and cabin systems. In addition, it boasts a functioning charging station and structures to mitigate the release of energy.
In the words of Gianluca Franchi, business development director of EN4, the facility is a “cutting-edge test rig, which has been designed to be a long-term asset supporting the Lilium Jet through certification and beyond.”
Lilium engineers are using a specially tailored software to chart flight profiles and run tests on the system. The company is collecting real-time data on those simulations, which will be shared with airworthiness authorities as evidence of compliance with its type certification requirements, it said.
“In this new lab, we test flights, charging, and simulate failure scenarios to ensure that our powertrain meets stringent aviation safety and reliability standards,” said Stephen Vellacott, chief technology officer of Lilium. “From first flight to certification and product launch, the lab enables us to demonstrate that our aircraft will be a world-leading product.”
Once power system testing is complete, the next major step for Lilium will be to fly the entire aircraft. The first jet off its production line will be deployed solely for ground testing, but the second is expected to make the model’s debut flight in early 2025.
The company so far has flown two Phoenix test aircraft, a full-scale, five-seat design intended to mirror the aerodynamics and hardware of its flagship model, and reached a cruise speed of 136 knots.
In June, it fired up the Lilium Jet’s engine to full throttle, marking another step toward crewed flight.
Like this story? We think you'll also like the Future of FLYING newsletter sent every Thursday afternoon. Sign up now.


Subscribe to Our Newsletter
Get the latest FLYING stories delivered directly to your inbox