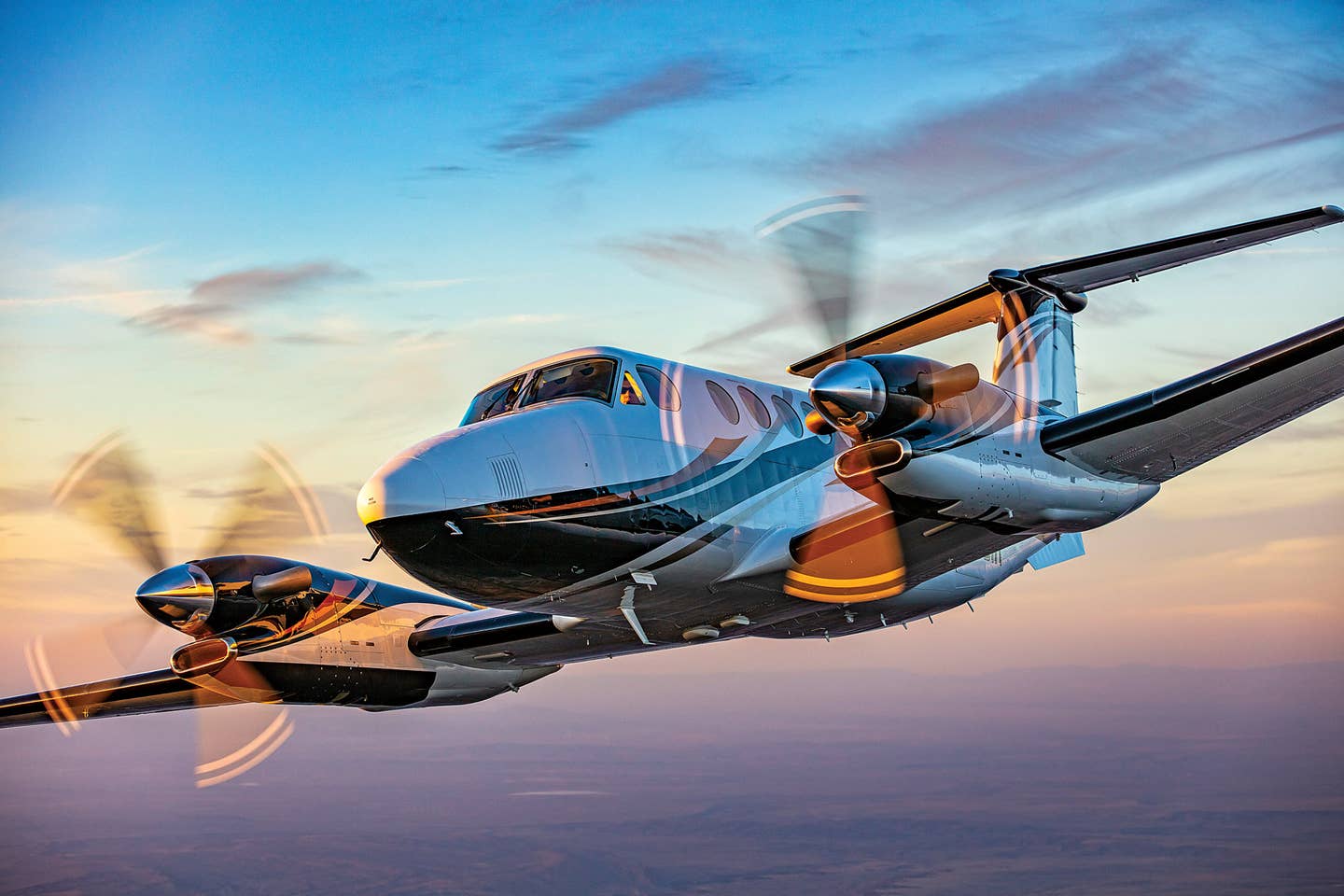
King Airs emerged from a rich Beechcraft heritage dating back more than 80 years. Textron Aviation
As I stood on the Textron Aviation ramp in Wichita, Kansas, for my first look at the company’s new turboprop flagship, the King Air 360, I slipped back in time to a different era and form of transportation: cars (muscle cars as they called them). My pal Lennie had just bought a brand-new, fire-engine-red Chevrolet Chevelle and, to my amazement, spent his first weekend with it stripping off many of the stock parts, mostly the ones no one could see.
He changed out the wheels, lowered the front end, added a growly exhaust, and yanked the automatic transmission in favor of a four-speed stick. The 1960s marketplace offered a plethora of options to add horsepower and torque, while owners maintained the stock look of the original machine as much as possible. The auto-parts store we visited in Chicago one Saturday was as vast as a Walmart today. Noticing my obvious awe at the incredible collection of mods for any kind of car, a salesman told me, “Kid, they only build this stuff for machines that have withstood the test of time.”
Beechcraft King Air 360 at a Glance
Back to the present in Wichita, I realized the King Air—a muscle airplane of sorts—has certainly stood the test of time, nearly 60 years since the first model 90 took to the air. With more than 7,000 King Airs having rolled off the Beechcraft production line since 1964, King Air magazine labeled it the most modified business airplane in history. Companies including Raisbeck Engineering, Garmin, BLR Aerospace and Blackhawk Aerospace wouldn’t have wasted time and money designing retrofit options for King Airs if they didn’t see a market—and they were right.
King Airs emerged from a rich Beechcraft heritage dating back more than 80 years. In the late 1930s, the Beech 18—of which 9,000 were built—became the guide for rugged, do-practically-anything airplanes. Those were followed by nearly 1,000 Twin Bonanzas, and then Queen Airs in the early 1960s. Because all King Airs share some version of the NACA 23000-series wing, they all owe part of their success to the Bonanza, where that airfoil’s use began. In fact, every Beechcraft product features a scaled or modified version of that 23000 airfoil. Over the years, the world eagerly purchased first the model 90, then the 100, then the 200, 250 and 260, and on to the 300 series that included the 350, 350i and now the new 360. This latest King Air was announced in August 2020 at block point change 1234 on the production line with deliveries beginning in November 2020.
On the ramp, most King Air 350 pilots probably won’t be able to distinguish a new 360 from a previous model from the outside. When I climbed on board, my eyes were drawn to the myriad ancient toggle switches and pop-out circuit breakers that have defined King Air cockpits for decades. Alex Hunt, a Textron Aviation technical marketing advisor and sales engineer on the 360, told me that in order to update any of that analog-era circuitry I’d noticed, Textron would have needed to reopen the original aircraft-certification documents with the FAA. Think big dollars for minimal return. He said, “We were very focused on reducing the pilot workload while improving passenger comfort.” That translated into “improve it where we could and not fix what wasn’t broken.”
That makes discovering how the 360 differs from the 350 a visual challenge. “We didn’t make any performance changes to the airplane,” Hunt said. “The powerplants are the same 1,050 shp P&W Canada’s PT6A-60As from the 350 and the same four-blade Hartzell aluminum props. With dual main landing gear, the 360 is still at home with rugged off-field landings.” In a pinch, the airplane can support its entire weight and operate on just one tire per gear. There’s also a Kevlar belly-plate option to cope with gravel runways, as well as a heavier version that comes with the landing gear from the Beech 1900 and tundra tires if needed.
The 360 retained the King Air’s elongated, oval-shaped fuselage, but the 360 added passive cabin-noise reduction versus the 350i’s active system. The 360 comes standard with 85 tuned absorbers working behind the scenes, sucking in all that annoying noise energy. The airplane also includes 11 seats: two in the cockpit, eight in the cabin and one belted potty seat. Some special-mission 360 models can seat up to 15. With a 1,550-pound useful load, flight-planning a King Air 360 is pretty simple. Fill the fuel tanks and all the seats, and with a 3,300-foot balanced-field-length runway nearby, trips of 1,500 nautical miles are a snap. How many twin-engine airplanes can handle that?
Jared Jacobs, the Textron Aviation operations pilot I flew with, told me during the preflight: “About two-thirds of the wing is flat for lower approach speeds. The aileron is about the other third of the wing that leads to some really nice handling characteristics. That NACA wing has great low-speed handling characteristics and good mid- to high-speed handling characteristics. We typically cross the threshold at about 100 knots. It also has a very good ice-carrying capacity because it was designed to [accumulate] less ice.
“The 360′s fuel system is pretty simple,” Jacobs continued, “[with] two mains in the outboard wing that gravity-feed the two auxiliaries inboard. Nothing tricky about moving fuel around. The engine nacelles each hold 300 pounds of baggage while the rear fuselage compartment next to the potty can carry up to 550 additional pounds. The wings and tail use pneumatic deicing. The props, the engine inlets, the windshield, the pitots and the fuel vents are all heated too.” He mentioned the T-tail has more than one advantage: “The 350/360′s [tail] helped create a wide CG envelope, so you’re pretty hard-pressed to create any CG issues when loading. There’s no need to tell passengers to sit in one seat or the other.”
The King Air was always designed to be flown by a single pilot, and most customers operate it that way. Up front, the Collins Aerospace Fusion avionics support that goal by bringing the Collins team’s airline experience to the flight deck, with three 14-inch touchscreens that include synthetic vision, TCAS II, dual FMSs and optional dual GPSs. The touchscreens allow the pilot to drag icons all over for graphical solutions, such as updating flight plans and diverting around any weather highlighted with the new multiscan weather radar.
Hunt said, “Textron also introduced the Innovative Solutions and Support’s ThrustSense autothrottles, which I believe is one of the finalists in Flying’s Editors’ Choice Awards this year.” When engaged, the IS&S autothrottle (A/T) system automatically provides full control of the engine power lever, from takeoff to short final and through a go-around when necessary. ThrustSense also includes aircraft-envelope protection should an engine experience a sudden reduction in power, as well as helping the pilot avoid the region near minimum controllable airspeed (VMC).
In addition to replacing those three analog pressurization dials beneath the throttle quadrant—which were older than many pilots flying the King Air 360 today—Hunt explained that the new automatic digital pressurization system is based on the one in the Cessna Citation CJ series. The automatic system eliminates the pressurization bumps common to older King Airs if the pilot didn’t keep up with the system, especially in the descent. Cabin-pressurization limits have increased from 6.5 to 6.8 psi, a full 10 percent change. At 35,000 feet, the cabin hovers around 9,600 feet. At 27,000 feet, the cabin altitude is 5,960 feet. Jacobs added, “The RVSM-approved 360′s sweet flying spot is between FL 280 and FL 310.” His flight-planning rule of thumb says, “At FL 300, the 360 will burn 300 pounds per side and move along at 300 knots.”
Check Out More Aircraft Reviews: We Fly
This King Air’s cabin rivals that of many medium jets and includes newly redesigned, locally produced cabin seats in a variety of tempting flavors. Adding to the cabin’s rich feel, the cabinets are now made of real wood veneer and tilt inward near the top to give passengers just a little more room as they walk through the cabin.
Hunt said the Textron team spent an enormous amount of time redesigning the seats using digital pressure mapping and SUV seating as a guide. “The test seats had dozens of embedded sensors to measure how a wide spectrum of bodies put pressure on them. The seats rack in all different directions and recline with adjustable headrests and armrests.” The cabin is outfitted with LED lighting, including pinhole accents that softly illuminate the lower side walls as well as the floor, cup holders, and power and USB plugs. The 360 now offers dual-zone climate controls, one for the cockpit and another for the cabin.
Textron Aviation quotes direct operating costs at $1,087 per hour based on flying 300 hours annually. Each purchase includes training for one pilot and one maintenance technician. Pilots head to FlightSafety International in Tampa, Florida, where they can earn their entire type rating in a Level D flight training device. List price on a King Air 360 is $8.39 million, a $640,000 rise from the 2020 King Air 350.
IS&S Autothrottle System
Surely the star of the King Air 360, at least from a pilot’s perspective, is the standard-equipment IS&S ThrustSense full-regime autothrottle that controls the power levers with just a touch of the button on the right power lever. The ThrustSense envelope protection is active during takeoff, climb and go-around should an engine experience a sudden reduction in power. It’s smart enough to turn on the igniters and rudder boost when needed and feather the prop on a bad engine—usually before the pilot even recognizes what might be happening. It also prevents the pilot from overtorqueing or overtemping the engines.
ThrustSense also provides VMC protection should the aircraft slow to anything near that speed. But this system’s envelope protection operates differently from what some pilots might expect. Rather than commanding the autopilot to pitch the aircraft’s nose over to reduce the angle of attack, the IS&S system slowly reduces power on the good engine to prevent a roll toward the bad engine as the aircraft reaches VMC. Hunt called the IS&S equipment an “elegant little engineering solution.” The autothrottle’s brain and most of the indications reside in the new IS&S standby attitude indicator that replaces the stock EFIS version sitting just below the glare shield.
Jacobs added: “In the event of a power loss, ThrustSense turns on the auto-ignition—thinking the engine may have flamed out—and attempts a relight. Assuming that does not work, the rudder boost kicks in with deflection proportionate to the power on the good engine. If engine rpm continues to drop, the propeller automatically feathers to reduce drag. Like in a jet, a 360 pilot only needs to maintain directional control and pitch up to climb.” The time from power loss to feather is about 10 seconds. Equally important, the IS&S system allows for use of the autopilot even through an autofeather. Jacobs said, “I do not know of another autothrottle system approved for single-engine operations.”
Autothrottles aren’t new, having been installed on airliners decades ago. I spoke to Tom Grunbeck, IS&S director of autothrottle programs, who said the company has been in the aviation business since 1988 and created the first practical RVSM altimeter, some 600 of which were installed on the Air Force’s KC-135 fleet and, later, on business and commercial jets. The IS&S’s first autothrottle installation on a business jet was on the Eclipse 500 in 2014.
Grunbeck said that while the King Air 360 was a relatively straightforward installation, “the challenge was fitting the actuation mechanism in that very tight throttle core and pedestal. One of the big breakthroughs was the actuation mechanism—there [are] two of them similar to what we designed for the Pilatus PC-12. Based on the safety and performance of the King Air, we came up with the [VMC] mitigation, which we felt was a huge added capability to the full regime system. We’ve only heard a lot of positive feedback. When ideas do come in, those are incorporated into the system with just software upgrades.”
Autothrottles in Operation
Pilots who’ve experienced autothrottles on medium or heavy jets might not think the IS&S system is all that impressive. But for an experienced King Air driver, especially as a single pilot, it will seem like heaven. Imagine arriving into the New York terminal area during bad weather at night when approach might have left you a bit too high for too long or changed the approach at the last minute, and then sequenced you behind a much slower airplane, and you’ll understand how busy a single-pilot cockpit can become. Just dial in the required speed, and the autothrottle handles the rest.
Just before lining up on Runway 19 Left at Wichita’s Eisenhower International Airport (KICT), Jacobs pointed out an important item: ensuring the throttle friction was set just right. Many King Air power reductions after takeoff have been traced to inadvertent power rollback—the result of the throttle friction being set too loosely. Many King Air pilots are apparently used to letting go of the throttles once they set the power. IS&S suggests pilots cover the throttles lightly on takeoff but not grab them, which might interfere with the servos.
I used the little finger on my right hand to engage the A/T switch as I began to add power. The IS&S system handled the rest of the work; all I did was steer. The CFI in me did find it tough to simply relinquish all control to the automation—at least on the first takeoff—but everything ran perfectly. Departure gave us a right turn to the west, and we blasted into the first cloud deck at about 1,200 feet, climbing at about 165 knots. As they cleared us above 10,000 feet, I set the altitude selector and rolled up the speed to about 200 knots for a flatter—though faster—climb. Within five minutes, I was comfortable with the A/Ts and switched speeds easily, watching the throttles find exactly the right power setting every time. We climbed to FL 300, and I swung the heading a few times as we dodged a few building thunderstorms and watched as the A/Ts gently increased the power in the bank and removed it at rollout. Having spent a couple of years flying a Garrett-powered turboprop, I tend to classify turboprops as either noisy or noisier, so I removed my headset for a check of the noise the passengers will experience. This King Air 360 had a trick up its sleeve—at FL 300, I heard almost nothing. I was really surprised at the quietness of the cockpit, and 360 buyers won’t want to skim past this feature. Back in the cabin, I had a normal conversation with Hunt, who had joined us for the two-hour flight. Thanks, Beechcraft. I give your passive noise-canceling system an A-plus.
I also performed a VMC demo as Jacobs retarded the left throttle. As the airplane began to slow, I continued adding back pressure. Approaching VMC, the right throttle began to roll back just as it was programmed to do. Sure, the airplane might not climb well, if at all, like this—especially if the gear wasn’t retracted and the flaps eventually raised—but the airplane certainly won’t roll over on its back the way that 350 did at Texas’ Addison Airport (KADS) in 2019.
But the most fun—though hardly what I’d call any work—were the first few ILS approaches we tried on the way back to 19 Left. Descending out of 10,000, the A/Ts were really smart—but not smart enough to slow the airplane below 250 knots if the pilot forgets for some odd reason. On autopilot, and approach control asked for 200 knots for a vector to follow traffic. I reached up, dialed 200, and watched the throttles come back as I reviewed the plate. As they descended us to 3,000, I heard, “King Air 360KG, turn right heading 160, join the 19 Left localizer, cleared ILS 19 Left approach.” All I did was crank in the new heading and adjust for the 130-knot approach speed, punch the approach button on the autopilot, and watch the aircraft shoot a perfect ILS. Wichita Tower cleared us for the option, so just before we reached minimums, we decided to go around. I pressed the GA button on the left throttle and watched the IS&S system add just the right amount of power. The flight director raised the command bars, and I followed them back around for another approach to a full-stop landing, cranking in speed updates as needed.
I think one reason the King Air line has been so successful is that they don’t excel at one particular mission, yet they possess something endearing them to pilots and operators across the board. The King Air is fundamentally a strong airplane, thanks to its evolution over more than 80 years of Beech aircraft construction. It’s also quite easy to fly, especially with the autothrottle to absorb some of the work for a single pilot.
Inside the IS&S Autothrottle
The IS&S autothrottle is made up of a standby display unit that replaces the aircraft’s stock backup EFIS display, actuators, a system annunciator, the A/T state light, an “A/T ENG” indicator, and a status LED. It has two primary operating modes: torque and airspeed.
The IS&S SDU includes standard pitch-and-roll, vertical-speed, airspeed, altitude, and nav data, as well as the A/T’s operational annunciations for speed and torque selections. The SDU also houses the A/T brain controlling the actuator assembly that physically moves the throttles with a gearless driveshaft mechanism that uses no physical clutch. Each of the power levers is controlled by a separate actuator/driveshaft assembly.
Annunciator
The operating mode, either “A/T speed” or “A/T torque,” appears in white. The annunciator text (“A/T ENG”) in green indicates when the A/T is engaged.
Status LED
The status LED will display: steady green when the autothrottle is engaged, flashing amber when the autothrottle has disconnected, and steady amber when the A/T disconnect must be acknowledged.
Protection Modes
A/T logic includes protection limits: flight-envelope, interstage-turbine-temperature, overtorque and airspeed protections. The A/T enters Protection Mode automatically when one of the protection limits is exceeded. The manually selected Operating Mode is restored when the protected condition is cleared.
Takeoff Mode: ThrustSense is engaged for takeoff and compensates for any engine surging. Takeoff mode is active until the system transitions into Climb Mode.
Climb Mode: The throttles automatically adjust for maximum continuous climb or torque as a function of altitude.
Go-Around Mode: The system automatically sets maximum safe power while maintaining full engine protection.
Airspeed Mode: This adjusts airspeed to the value commanded through a manually selected speed change.
Engine Out Mode: If Takeoff, Climb or Go-Around modes are selected when an engine fails, the A/T controls the good engine by transitioning into Engine Out Mode. A/T Engine Out will be annunciated in amber, and the A/T will command maximum available torque on the operating engine. The pilot may still adjust the target torque setting as long as the airspeed is above VMC. If the airspeed falls below VMC, the A/T reduces torque as needed to avoid overpowering the rudder’s authority. Below VMC, the target torque value will be blacked out on the SDU and cannot be manually adjusted.
This story appeared in the August 2021 issue of Flying Magazine

Subscribe to Our Newsletter
Get the latest FLYING stories delivered directly to your inbox